Description
This satin black polyester paint-coated aluminum coil blends aesthetics and functionality for roofing sidings and gutters. The smooth, low-gloss satin finish enhances architectural appeal while resisting fading, chalking, and UV damage. Crafted with durable polyester coating, it offers superior corrosion resistance, ideal for outdoor exposure. Lightweight yet robust, the coil ensures easy forming and installation, reducing labor costs. Its uniform black hue complements modern and traditional designs, while the corrosion-resistant aluminum substrate (typically AA1100 or AA3003) guarantees long-term durability. Suitable for residential and commercial projects, this coil delivers weatherproof performance, low maintenance, and a sleek, timeless look for roofing components.
Specification
Embossed Coated Aluminum Coil |
Product | Embossed Coated Aluminum Coils |
Thickness | 0.2-1.0mm |
Diameter | 1500mm |
Material | AA3105 AA3003 AA1100 AA1050 AA1060 |
Temper | H24 etc |
Inner Diameter | 500 |
Color | RAL colour |
Coating thickness | PE coating |
| PE Paint Coating : Not Less Than 28um |
Packing | Export Standard Wooden Pallets |
Payment Terms | L/C at sight or 30% T/T in advance as deposit |
MOQ | 8Tons Per Specification |
Delivery Time | Within 45 Days |
Loading Port | Shanghai Port |
Application | Roofing,Gutter,Siding, Joint. Wall,Truck,Container |
Application of Satin Surface Black Polyester Paint Coated Aluminum Coil
Architectural Cladding
Interior Decorations
Doors and Door Frames
Furniture Manufacturing
Window Shutters
Signage and Displays
Exterior Trim and Molding
Ceiling Systems
Garage Doors
Roofing Applications
Exhibition Stands
Transportation Industry
The difference between 3003 aluminum Alloy and 3105 aluminum Alloy
Both 3003 and 3105 are aluminum alloys, but they have some differences in terms of their chemical composition and properties. Here's a comparison between the two:
3003 Aluminum Alloy:
Chemical Composition:
3003 aluminum alloy is primarily composed of aluminum (about 98.6%), manganese (1-1.5%), and trace amounts of other elements.
Properties:
Good corrosion resistance, making it suitable for various applications.
Moderate strength, not as strong as some other aluminum alloys.
Excellent formability and weldability.
Commonly used for general-purpose applications, such as cooking utensils, kitchen equipment, and heat exchangers.
Applications:
Roofing materials, cooking utensils, kitchen equipment, heat exchangers, and other general-purpose applications where corrosion resistance and formability are important.
3005 Aluminum Alloy:
Chemical Composition:
3005 aluminum alloy is primarily composed of aluminum (about 98.6%), manganese (1-1.5%), and a small amount of magnesium (0.6-1.1%).
Properties:
Improved corrosion resistance compared to 3003, especially in more aggressive environments.
Good formability and weldability.
Moderate strength.
Often used in applications where increased corrosion resistance is required compared to 3003.
Applications:
Similar to 3003, 3105 is used in general-purpose applications. However, it is preferred in situations where enhanced corrosion resistance is necessary, such as in marine environments.
Key Differences:
Corrosion Resistance:
3105 generally offers better corrosion resistance compared to 3003, especially in more challenging environments. This is due in part to the inclusion of magnesium in the alloy.
Strength:
The strength properties of 3003 and 3105 are relatively similar. Neither is known for high strength, but they are suitable for applications where strength is not a critical factor.
Applications Focus:
Both alloys find application in general-purpose uses. However, 3005 is often preferred when increased corrosion resistance is a priority.
Magnesium Content:
3105 contains a small amount of magnesium, contributing to its enhanced corrosion resistance. In contrast, 3003 does not contain magnesium.
Common Uses:
Both alloys are commonly used in the manufacture of heat exchangers, cooking utensils, kitchen equipment, and other applications where corrosion resistance and formability are important.
In summary, while 3003 and 3105 aluminum alloys share similarities in composition and application, the inclusion of magnesium in 3105 provides improved corrosion resistance, making it suitable for applications where exposure to more aggressive environments is a concern. The choice between the two would depend on specific project requirements and the level of corrosion resistance needed.
Production Line Photos:


Quality Control
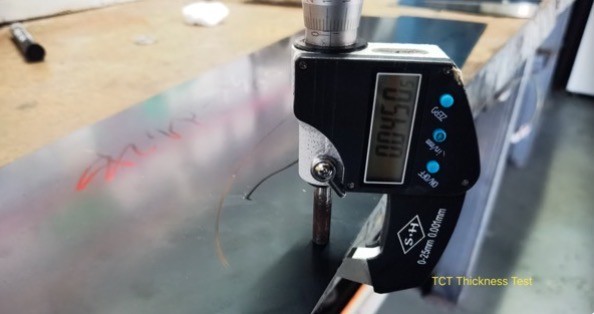
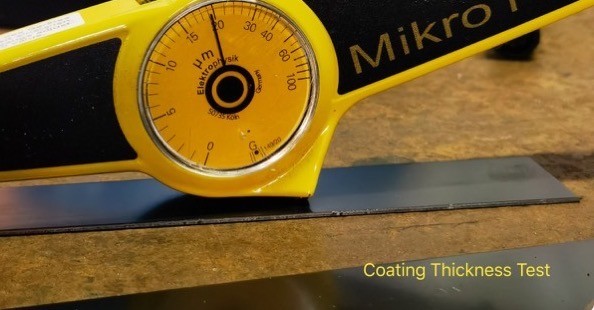
If you are interested in our embossed aluminum products, please feel free to contact us!
Our embossed aluminum sheets feature unique texture designs, combining aesthetics and functionality, and are widely applicable to multiple fields such as architectural decoration, furniture manufacturing, and packaging.
|
Satin Black Polyester Paint Coated Aluminum Coil used in Aluminum Roofing Sidings and Gutters Images
|